Digitization of the temperature control unit
Innovative, model-based thermal industrial systems: Tool Temp AG and three institutes of engineering at the FHNW realized a novel control technology concept.
- Predictive process control
- State variables
- Injection molding and Moldflow simulation
Tool Temp AG from Sulgen (TG) manufactures temperature control units for the plastic, chemical and pharmaceutical industries. These devices have a robust and simple analog control technology, which, however, has potential for improvement regarding a development and implementation of Industry 4.0 and a digitalized process chain. The realization of an intelligent process control for the temperature control of injection molds should help Tool Temp AG to offer the customer energy-efficient systems with the possibility of online diagnosis, monitoring and control.
The aim of the project was to optimize the temperature control process in injection molding regarding more energy-efficient use with the aid of a simple digital control loop. Using the findings from filling and temperature field simulations, the respective dependencies of the individual process-dependent and dynamic state variables were to be mapped in a predictive control model and thus the process optimally controlled. A further objective was to include all essential parameters in relation to customer-specific wishes and requirements to enable continuous monitoring of the injection molding process.
All essential state variables were successfully included in a mathematical model and described with the help of a so-called "predictive control loop". The model-based prediction of the system behavior and the formulation of an optimization task to be solved is carried out for a specific point in time and continues to apply beyond this point based on the findings from many simulations and measurements. In this way, process control can be implemented in a relatively cost-effective manner without significantly interfering with the proven technology of analog temperature control.
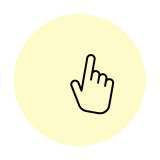
Client | Tool-Temp AG, Sulgen |
Execution | |
Duration | 2 years |
Funding | |
Project Team | Prof. Dr. David Zogg, Steffen Thierer, Andreas Zogg, Jonas Asprion, Halime Philipp |