LeiWaCo - Development of a lightweight tank for cryogenic hydrogen
Hydrogen plays a central role as an energy storage and carrier in the ongoing energy transition. The aim of the project is to develop a cost-effective, high-strength, lightweight hydrogen tank made of fiber composites that has been specially developed for transporting liquid hydrogen.
- Composite
- Hydrogen storage
- Thermoplastic winding
In addition to large-scale hydrogen transport via pipelines, there is a growing need for versatile solutions for smaller-scale hydrogen transport across various industries, including filling station supply, rail operations, and port and airport logistics. Currently, compressed gas storage tanks, commonly known as «large cylinders», are used for these purposes, with a typical capacity of about 500 kg of hydrogen. While effective for small to medium quantities of hydrogen, alternative solutions are needed for larger quantities and longer transport distances.
This project sets out to develop a cost-effective, high-strength lightweight hydrogen tank constructed from fiber composites specifically designed for liquid hydrogen transport. The objective is to create a cross-industry logistics solution in the form of a container-based transport and supply unit. Additionally, the consortium aims to adapt these innovative technologies for tanks used in road transport, shipping, rail transport, and aviation.
One of the primary challenges in developing cryogenic fiber composite tanks is ensuring their tightness, which can be affected by thermally induced microcracks in the material. To address this challenge, the project introduces a novel approach involving the use of thermoplastic materials in combination with thin-film technology. This approach encompasses the development of new production methods for the semi-finished product, testing methodologies, design and calculation methods, as well as corresponding production technologies.
Compared to existing large cylinders, the tank to be developed in this project aims to achieve significant performance improvements:
- Increase the capacity by approximately 500 kg per 2,500 kg.
- Limit the weight of the entire container to 10 tonnes.
Furthermore, compared to traditional metallic tanks for liquid hydrogen, the tank made of fiber composites offers several advantages:
- Lower production costs due to a highly efficient winding process with in-situ consolidation.
- Reduced weight with the same internal pressure of the tank.
- Elimination of hydrogen embrittlement often observed in welded joints.
- Increased compressive strength due to the mechanical properties of fiber composites, allowing for higher pressure within the tank.
Compared to previous cryogenic tanks made of CFRP (carbon fiber-reinforced polymer), the project aims to extend the service life from approximately 40 refueling cycles in space travel to significantly enhance fatigue strength.
This project brings together a diverse group of partners, each contributing their expertise in various aspects of material development, manufacturing, and technology applications.
The project aligns with the objectives of the Energy Research Programme, focusing on indirect storage of renewable electricity in the form of green hydrogen and the development of hydrogen technologies, particularly storage and transport technologies. By creating innovative solutions for hydrogen storage and transportation, this project can significantly reduce greenhouse gas emissions and contribute to achieving climate change targets.
The project combines cutting-edge technologies, including the use of thin-ply materials, thermoplastic matrix materials, and in-situ consolidation, to develop advanced hydrogen tanks. These innovations have the potential to transform the efficiency and performance of hydrogen storage and transportation.
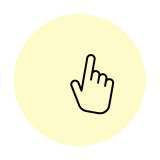
Client | |
Execution | |
Duration | 3 years |
Funding | |
Project Team |