I’ve got the power!
Our new motor housings and wheel units are here!
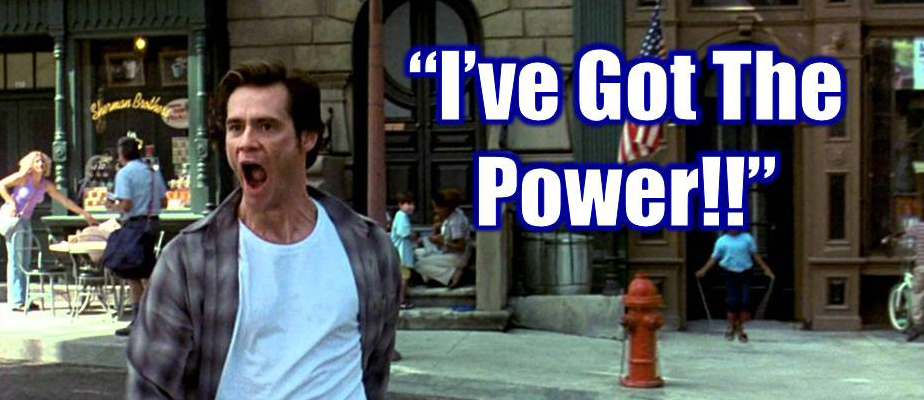
This monday, our freshly manufactured components for the wheels arrived. Thank you FHNW Workshop Brugg/Windisch for getting them done so nicely! With the new parts, the wheel housing is made of two major parts. The inner part holds the electric motors, gearboxes and encoders, while the outer part glides over the inner part and is fixed to the 3D printed wheel. With the new mechanical parts, we ensure our sponsored maxon motors can reach their full potential.
While the design is similar to the first version, our mechanical engineering student Constantin has heavily optimized the design.
Constantin, what wasn’t good with the old design and what did you want to improve for the second iteration of the wheel?
The old wheel units used ball bearings, which were quite big and very heavy. The design was a good first iteration to test the rover, but wasn’t really feasible for the finalized product. Furthermore it was quite complicated to take it apart and assemble it again, which used up a lot of time when we tried to test stuff with the motors. The first test also showed that we needed motor encoders, which wouldn’t fit in the old units.
The 3D printed wheels which were made with a flexible filament called TPU were also not ideal, as they were too soft.
How did you achieve these improvements?
With the new design, the outer part is made of POM and directly acts as a sliding bearing. This saves a lot of space in the radial direction. Together with the no longer needed ball bearings, the weight has been reduced by over 1 Kg per wheel unit. The part is also shorter in the axial direction, with the encoder now being attached on the rear side of the motor outside the wheel. With a simplified design, it is now also easier to disassemble the wheel and access the motor.
To improve the 3D printed wheel, we used two filaments. The inner circle of the wheel is made with PETG, a filament for high strength mechanical uses and an outer ring with the same flexible TPU as before, but a more rigid design structure. You can see the FEM simulation below:
What does that mean for the rest of rover? How much power can we use now?
The final design makes the rover a lot lighter. The new wheel design is over 2 Kg per wheel lighter, resulting in a over 8 Kg weight reduction. Furthermore, the encoders ensure the electric motors from maxon can now reach their full potential, even with very slow speeds or at standstill. That means we have access to over 20 Nm torque per wheel!
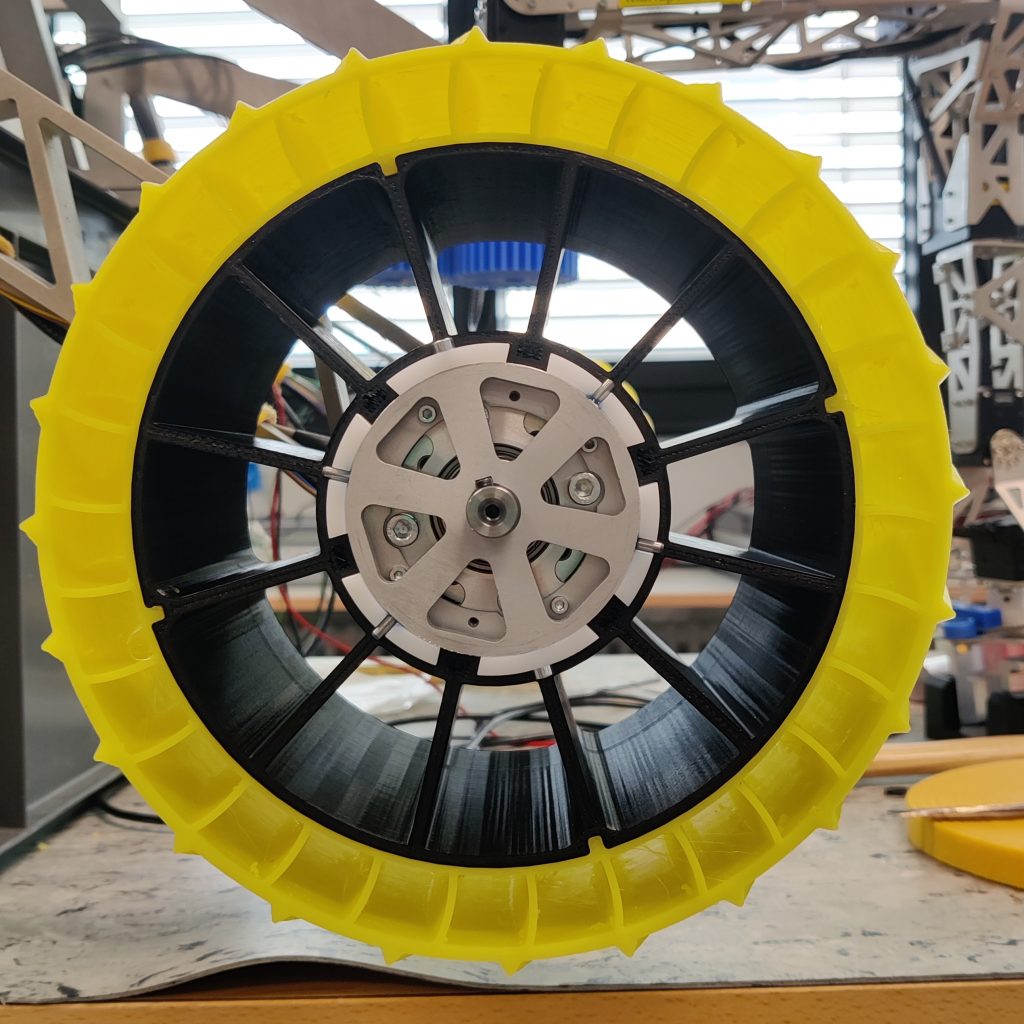
With the wheel units now being finished, we can start doing our first outside trials in the next couple of days. Make sure to check in to the blog soon to see the results. Also check out maxon for their awesome products:

Comments
No comment posted about I’ve got the power!