Quest for the Perfect Topology
So, what is topology optimization? It’s basically some engineering magic that turns boring, oversized designs into an exciting looking, lightweight nightmare for machinists. In more serious terms, topology optimization is a mathematical method which optimizes the structure of a given object by removing as much material as possible while retaining enough strength to withstand the specified loads.
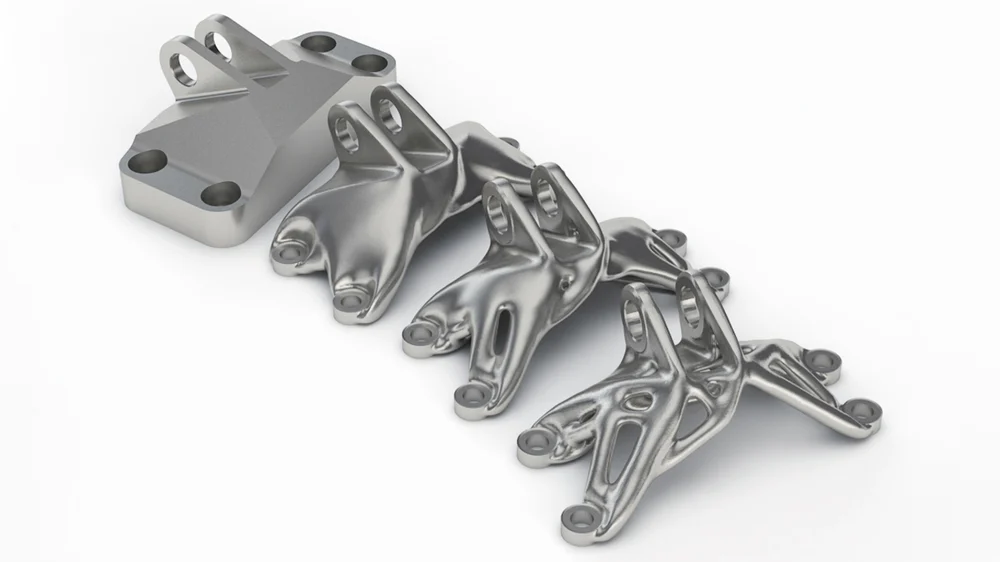
This is especially useful for lightweight applications, but it also comes with a downside: The geometry generated by a topology optimization software is often very complex, and many topology optimized parts would have been impossible to manufacture with traditional manufacturing methods. Only recently, since the rise of 3D printing, topology optimization has gained in popularity. While 3D printing has its own downsides, one of its biggest advantages is that it can produce almost any part, no matter how complex the geometry is.
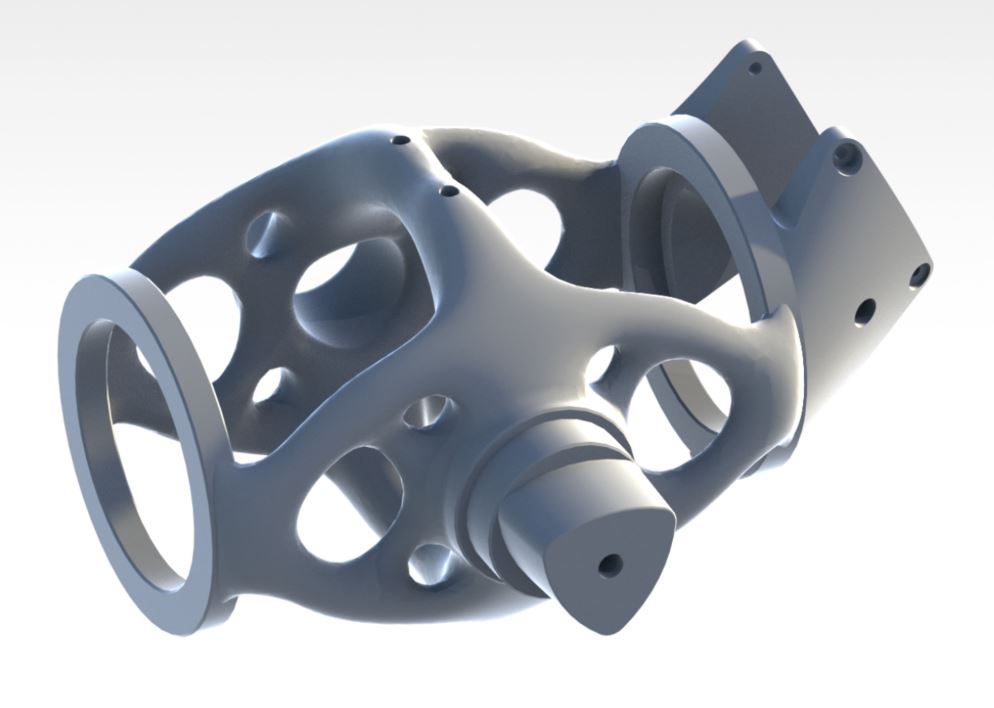
Due to our in-house 3D printing capability and the weight limitations for our Rover, we implemented topology optimization on several different components like the camera tower or the jaws of the manipulator. The largest part was the hinge component, which connects the upper arm to the lower arm. It has to transfer a relatively high torque of 70Nm. At the same time, it needs to be as light as possible, since every gram we add to the arm, results in a decrease of lifting capability.
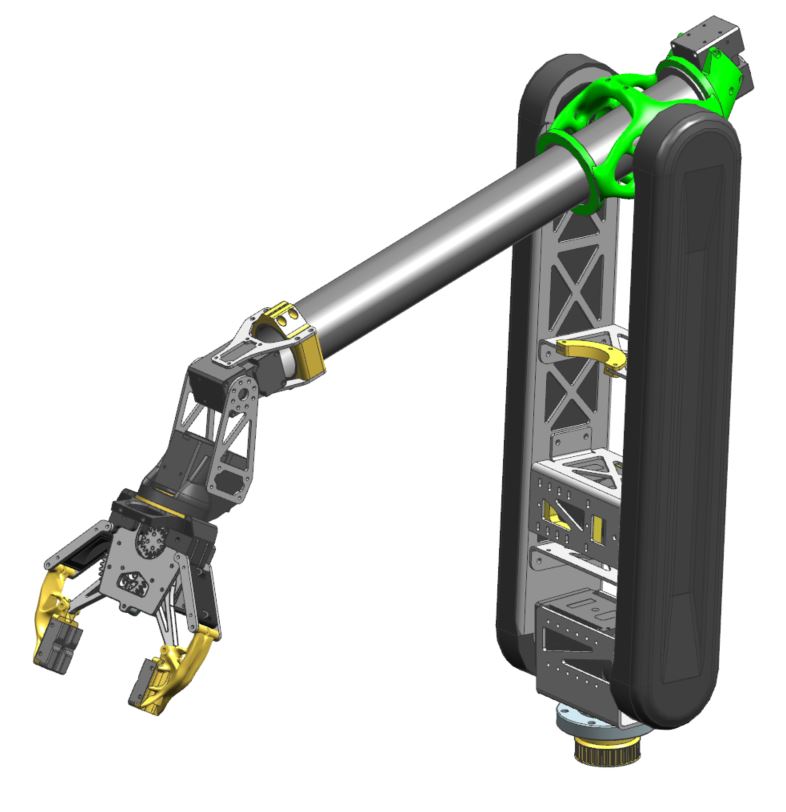
First, we needed an initial model. This served as a Base for the optimization. Since topology optimization can only remove material from the initial model, and it can not add any material to it, the initial model had to be more than strong enough to handle the expected loads. If the initial model can’t handle the loads, you can’t optimize it (at least not with this method).
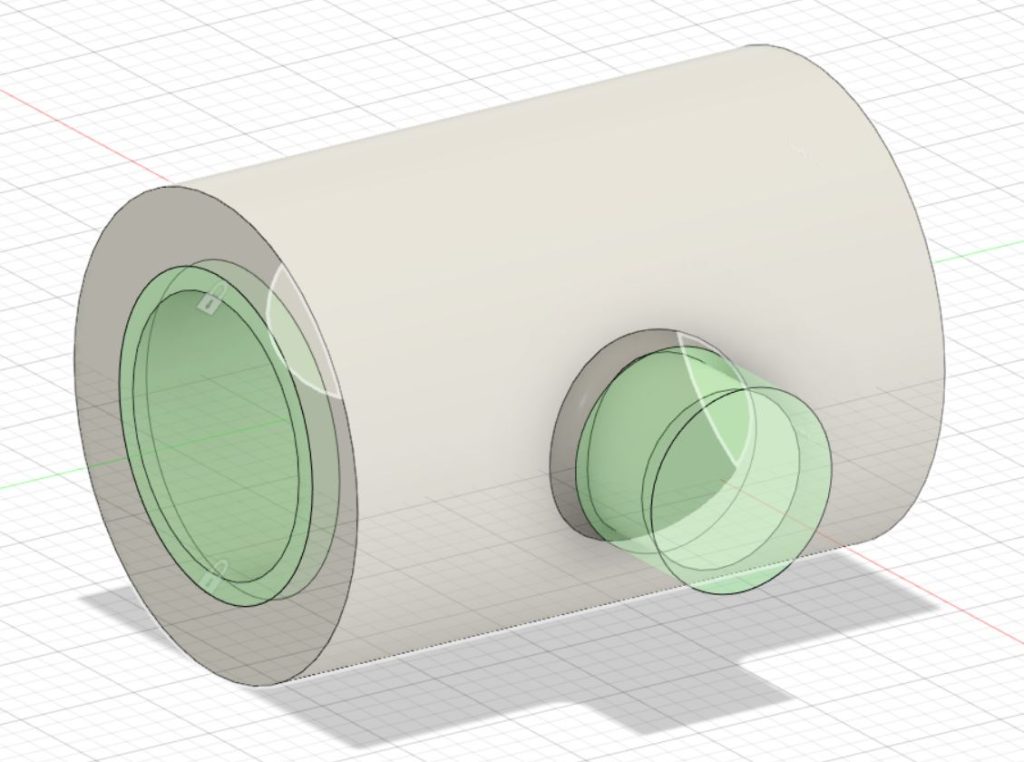
Once we had an initial model, we defined all the expected loads, the mounting points and the desired material. Then our topology optimization software (Fusion360) analyzed the model using the finite element method. This splits the model into a bunch of small elements and with regard to the previously specified loads, the software can calculate the stress in every single Element. Now the real magic can happen: The optimization software ranks all the elements from the lowest stress to the highest stress, and the elements with the lowest stress can be removed. You basically “fire” all the lazy elements but all the “hard-working” elements can stay, which leads to a very efficient material distribution. This way we were able to remove about 80% of the material, which reduced the weight of the part from 1250g to 250g. At the same time, the safety factor only decreased by a relatively small amount (from 2,5 to 1,8). This means we could have optimized it even more, but we decided to stay with a safety factor of 1,8 in order to decrease the risk of failure.
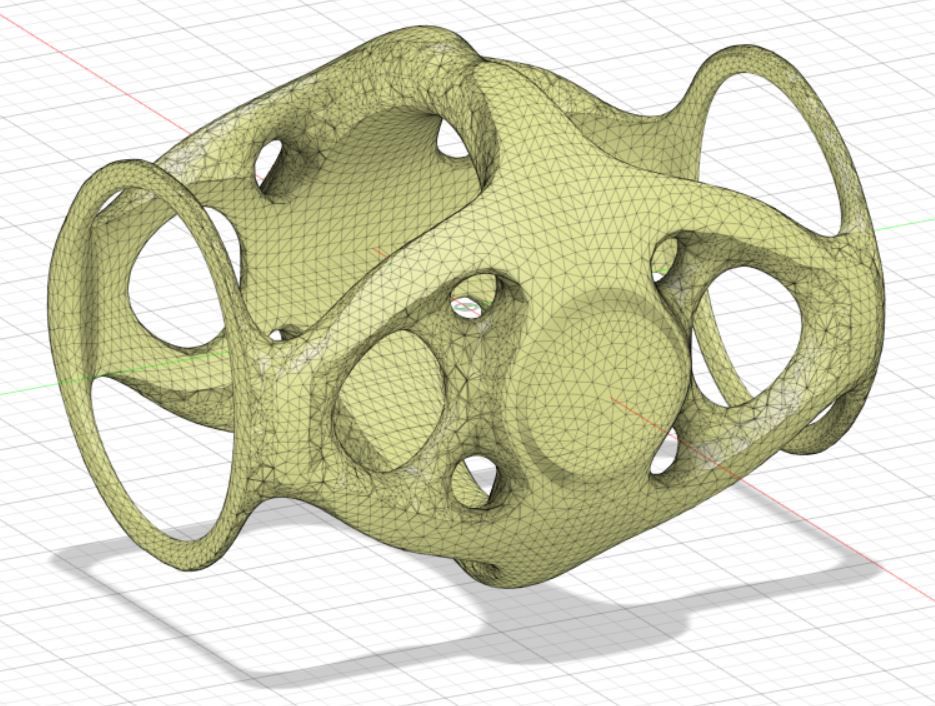
Special thanks to Sintratec, who let us print the part on their SLS 3D printer, which has much better tolerances and higher quality than our own FDM printer.
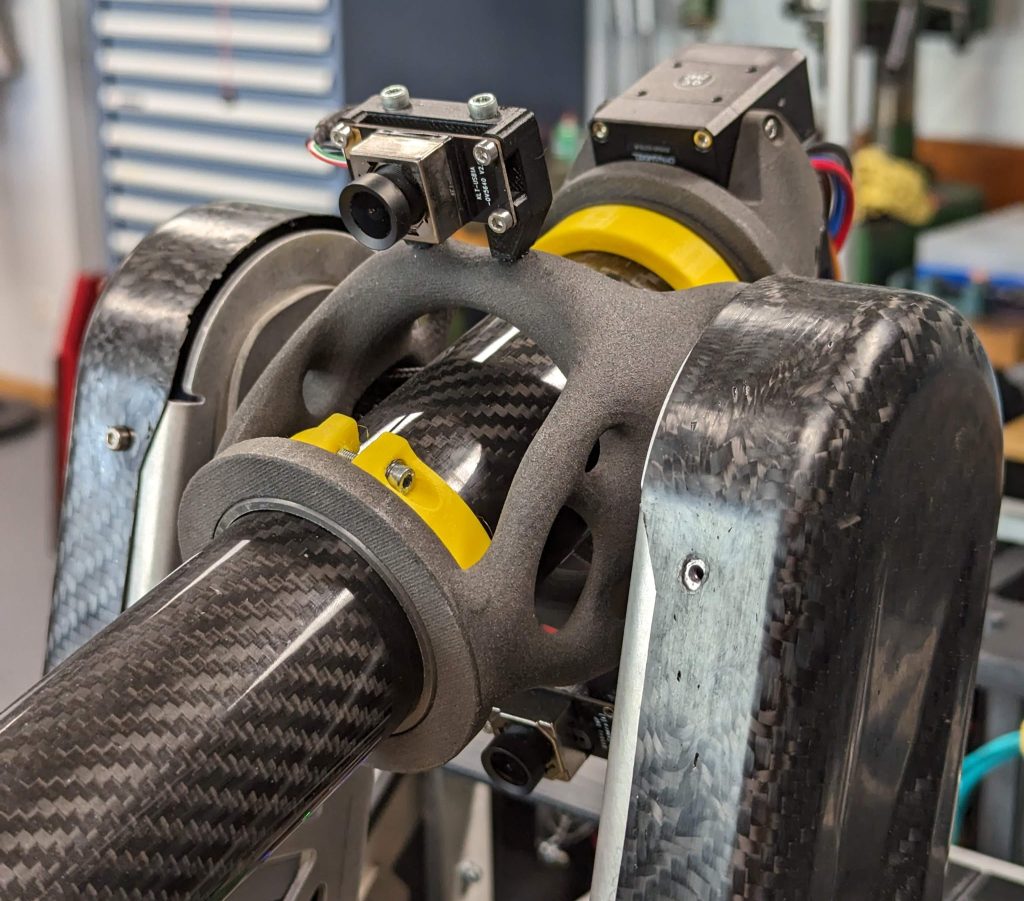
Comments
No comment posted about Quest for the Perfect Topology