Einsatz von Naturfaserverbundwerkstoffen für Leichtbauanwendungen
Naturfaserverbundwerkstoffe gehören zu den Kernkompetenzen des Instituts für Kunststofftechnik der Hochschule für Technik FHNW. Gemeinsam mit der Fa. BCOMP wurde die Gesamtperformance dieser Verbundwerkstoffe verbessert.
Abbildung 1: Flachsgewebe
Extrusion, Imprägnieren, Compoundieren, Materialmodifikation, Umspritzen
Flachsfasern sind aufgrund der hohen Steifigkeit und der geringen Dichte hervorragend für den Leichtbau geeignet. Die Nutzung nachwachsender Rohstoffe führt neben dem Vorteil der langfristigen Versorgungssicherheit zu einer positiven CO2 Bilanz am Ende eines Produktlebenszyklus.
Als Matrixmaterial verwendet BCOMP sowohl duroplastische Systeme als auch thermoplastische. Aufgrund der geringen Temperaturbeständigkeit der Fasern beschränkt sich die Auswahl der Thermoplaste auf Materialien mit einer niedrigen Schmelztemperatur. Der Fokus in der Zusammenarbeit mit der FHNW lag auf den thermoplastischen Composites. Die duromerbasierenden dienten als Referenz.
Das Institut für Kunststofftechnik FHNW arbeitete daran, das Matrixsystem durch spezielle Additive für die Naturfasersysteme zu optimieren, den Imprägnierungsgrad der Flachsfasern und die Faser-Matrix-Haftung zu erhöhen und damit die Gesamtperformance des Verbundwerkstoffs zu verbessern. Hierfür musste auch ein neues effizientes Fertigungsverfahren entwickelt werden, welches eine kontinuierliche Fertigung von powerRibsTM im km-Massstab ermöglicht.
Die von Bcomp entwickelten powerRibsTM stellen durch ihre gitterartige Struktur eine Revolution in der «Composite Welt» dar. Durch imprägnierte Flachsgarne entsteht eine Verrippung, welche nicht nur zu einer höheren spezifischen Steifigkeit, sondern auch zu verbesserten Dämpfungseigenschaften des Bauteils führt. Das mögliche Anwendungsspektrum dieser Technologie erstreckt sich über viele Bereiche und mittlerweile wurden die Projektergebnisse genutzt, um die Materialformulierung und Fertigungstechnologie zu industrialisieren. Zum Beispiel werden Autositze mit amplitexTM Panels hergestellt, die auf der Rückseite mit powerRibsTM versteift werden. Dadurch wird nicht nur Gewicht gespart und die Autos ökologischer, sondern Schwingungen können deutlich reduziert und Energie im Falle eines Unfalls besser absorbiert werden.
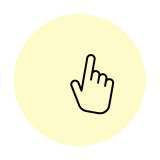
Auftraggeber | |
Ausführung | |
Dauer | 2 Jahre, 2016 bis 2018 |
Förderung | |
Projektteam | Christian Rytka, David Botor, Moritz Thommen, Kunal Masania, Jesus Maldonado, Clemens Dransfeld, Julien Rion |