SuMa - Sustainable materials for 3D printed composite parts
High-performance composites exhibit excellent mechanical and chemical Howev-er, the comparably high costs and the negative climate balance, especially for car-bon fiber composite parts, are critical and will be even more important in future applications. The project SuMa focuses on product development of sustainable composite materials for 3D printing.
- Recycling of carbon fibers
- Life cycle analysis
- Additive manufacturing
3D printing, an additive manufacturing technology, is believed to deliver on those demands for sustainable manufacturing because aspects like near net shaped, pos-sibility to do local on demand manufacturing are apparent. Besides, there is a po-tential to shift from petroleum-based materials towards biobased polymers, natu-ral fibers and or recycled /reclaimed fibers to reduce CO2 footprint or even to apply negative emission material (to save CO2 into products) and to apply circu-larity.
The project focuses on the product development of sustainable materials on dif-ferent levels (biobased, natural fibers, reclaimed fibers) for the additive manufac-turing technology of 9T Labs. For these materials, especially recycled or natural fibres which are typical discontinous in combination with new biobased polymers a high uncertainty exists about their performance but as well about their pro-cessability. Therefore 9T Labs needs the expertise in polymer science from the FHNW. By implementing a knowledge-driven approach to design for circularity, we can facilitate a transition toward carbon-neutral applications.
Our project investigates the development of short fibre-reinforced 3D printing filament with various reclaimed carbon fibre content, as well as the development of a continuous tape filament with reclaimed carbon fibre. Combined with reclaimed carbon fibre, short and high-oriented composite materials were developed, characterized and used in the three end user applications.
The objective of the project is to develop new types of materials, related to an aerospace, an automotive, and a sporting goods use case. The study concludes with a life cycle analysis of specific benchmark applications, illustrated in Figure 1.
Recycled and natural fibres are typical discontinuous fibers and in combination with new biobased polymers, pose a high uncertainty in terms of performance and processability. One reason is, that the load-carrying capacity is highly dependent on the shear stress distribution and the orientation degree of the fibres.
Quasi-static tensile tests demonstrated that an increase in fibre content leads to an increase in tensile strength and stiffness. The 3D printing process helps the realignment of short fibres, resulting in a 10% increase in tensile strength. The recycled carbon fibres showed the same properties as their virgin counterparts. Compounds with 35w% carbon fibre were possible.
The project broadened the scientific understanding of discontinuous fibre topology (natural fibre or rCF) related to additive manufacturing. Process related parameters could be related to the mechanical performance of the final component. The findings of this project promote the holistic design-for-circularity approach and a shift towards carbon neutral production of composites.
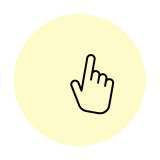
Client | |
Execution | |
Duration | 2.5 years |
Förderung | Innosuisse |
Projektteam | Lucian Zweifel, Julian Kupski, Anton D’Auria, Christian Brauner |